为了更好地理解这个方案,还需要从理论的部分说起。20世纪初产生的科学管理理论,通过对工厂内工人的操作过程进行研究,开始形成了标准化的生产作业管理。科学管理也伴随着以福特为代表的大批量制造企业的崛起而迅速发展,这也是后来工业工程(industrial engineering 简称 ie)专业建立的基础。二战结束后,ie 的工具和方法传播到了日本,日本丰田汽车在吸收了 ie 工具的基础上,结合超市里商品被消耗后才由售货员补充的概念,创新性地提出了拉动式的生产方式,形成了丰田生产方式(toyota production system,简称 tps)。20世纪90年代,《改变世界的机器》这本书对丰田和通用合资的 nummi 工厂进行研究,首次提出了精益生产的概念,讲述了精益生产的方式——「精益的本质即消除浪费」
精益生产的本质和核心是消除浪费,通常把其中常见的浪费称为:timwood——搬运(transport)、库存(inventory)、动作(motion)、等待(wait)、过度生产(over production)、过度工艺(over process)、不良品(defects)。常见的七种浪费根据不同的类型,可以分为数量、质量和人员的浪费,但归根结底是属于时间的浪费。精益就是在通过不断地消除非增值的时间,扩大增值时间占比的方式帮助企业提高效率。
多品种小批量的特点而多品种小批量的产品行业,往往存在着生产周期长、换型频次多、紧急插单情况频发、生产计划变更频繁、标准作业不易制定等问题,而要想解决这些问题,如果只是在生产现场推行精益生产的改善工具的话,并不能很好的消除生产管理过程中的全部浪费,无法从根本上解决多品种小批量企业的痛点。对于多品种小批量的产品生产线而言,打造一条可同时生产多种产品的高柔性化生产线以应对多品种间的频繁切换,才是打开多品种小批量生产线的正确方式。
快速换型和均衡计划的解决方案可帮助多品种小批量的生产线有效推进精益生产以快速换型和均衡计划为主要内容的精益解决方案,不只在生产现场进行改善,而是梳理客户订单开始至交付产品全过程的价值流,通过建立后补充式生产机制,优化换产改善过程,调整生产订单的排产方式,最终实现柔性化的生产线,以满足多品种小批量的产品需求,使之具备数字化的基础。
以西门子北京数字化体验中心和西门子成都数字化工厂为例,数字化的背后是一整套基于精益理念的生产管理优化体系。这里举一个实际的改善案例,帮助大家理解如何在多品种小批量的产业实施快速换型和均衡计划为主要内容的精益解决方案。
某电子研究企业 s,以射频单元为主要产品,并负责生产众多种类的小批量研发型创新电子产品。主要的射频单元组件包括一个铝合金壳体和内部多层电路板,生产流程根据产品层级分为,微组装、板级和装配三个工步。微组装生产出部分自制元器件,经过板级组的表贴、电装和调试工作组成半成品,并最终在装配线完成装配工作。其中板级同时存在大量表贴作业(一种机加工自动加工操作)和手工电装作业。因除生产主要产品射频单元外,同时需要负责大量研发创新产品所需小批量的半成品的生产,板级组存在生产计划不均衡、前后工序衔接不顺、表贴设备可动率低、量产产品批量大、表贴排产插单量大以及产品流动路径混乱等问题,成为制约生产效率提升的瓶颈,亟待优化改善。
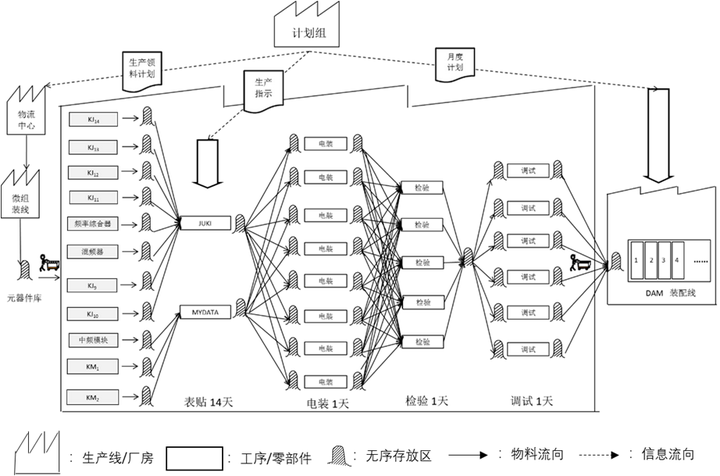
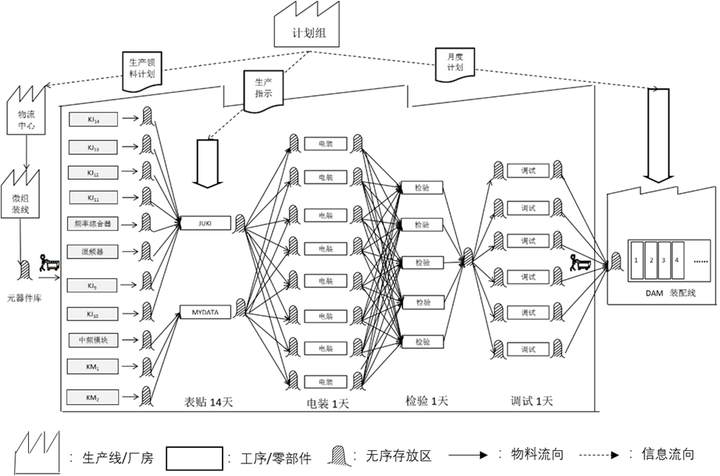
通过以上物与信息流动图分析板级线存在的主要问题包括:
表贴设备换产时间长,停机时间长。量产产品换产时间约 40′30″,研发创新产品项目需求量小,各项目差异较大,平均换产时间约 3h。表贴设备排产批量大,拖单插单情况严重。现有排产由调度人员根据各产品生产计划的完成紧急程度凭经验制定,所排计划未充分考虑物料是否齐套等生产实际,出现了大量无法及时完工的产品造成延期拖单的情况。物流路径混乱复杂。各工序之间的物流关系复杂,量产产品与创新产品的物流路径混乱不明确,无法判断各项目的生产状态是否正确。在制品多,过程周期时间长。各工序间在制品拉长了过程周期时间,且创新的小批量产品生产过程周期波动性较大。现场浪费情况普遍。各工序间均存在寻找元器件、作业人员步行过多、搬运距离过长、返修产品数量众多等不同程度的浪费。那如何以快速换型和均衡计划为主要思路进行改善呢?
答案是先明确描绘出生产线理想化的应有状态,将理想状态与实际状态进行对比,找出其中的差异点,差异点即为无法达到理想状态的原因,后对理想和实际的差异点进行改善,使生产线逐渐达到理想化状态。
板级线的理想状态是,打造量产产品与创新产品各自形成整流化的加工单元,根据各种量产产品各自的每日需求量实现每日均衡化生产,换产时间缩短至分钟级成为一触式换产,消除员工作业中的浪费,努力实现一人工的同时减轻作业负担。
结合板级线的生产现状,分析确定改善重点为「生产方式」、「计划排产」、「快速换产」及「作业改善」。考虑从整流化和均衡化的角度进行生产线改善,达到生产线的准时化。推行准时化的关键在于使工序内和工序间的物料、信息等能够有效地快速流动,在制品数量降到最低,各工序的产品处于同时流动的状态。整流化是以生产过程中的物流路径为出发点,按物流路径和加工顺序布置工序位置,以提高物流效率降低管理难度。结合板级线设备采购限制等约束条件,对板级线生产过程进行整流化,梳理明确物流路径。
改善步骤如下:
一、生产方式改善——建立后补充机制
为了达到在必要的时间只将必要物品的必要量供应给各工序的准时化状态,需要转变原有的计划式生产,逆转生产的指示信息流向。创新产品种类较多且需求量存在不确定性,而对于需求数量较多的量产产品建立生产后补充机制。后补充机制即后工序在必要时间去前工序领取必要量的必要物品,前工序只生产被领走的部分。
设立店面。通过建立质检人员巡回检验的方式,缩短板级线工序间转运时长,由原有1天缩短至 0.5 天,在工序间设立店面,各店面存量为下道工序 0.5 天的需求量。确定转运容器的规格和收容数。根据产量求出容器具需求量且为便于目视化管理,修改原有转运容器大小,转运容器数从原有 40 件修改为 20 件。确定领取的方式、人员、时间和数量。板级线中各工序均指定一人负责物料的领取转运,印有工位、规格、数量和编号的空盒在板级线的后补充机制中一定程度上起到了看板的作用。二、快速换产改善——smed
为了实现均衡化生产,必须针对大批量生产的表贴工序,减少其生产批量,提升灵活应对变化需求的能力,缩短过程周期时间,追求精细快速的流动。快速换产是追求小批量化的必要条件。尤其是在混流生产下,频繁切换生产品种的小批量生产对换产时间的要求更高。量产产品的增值工作时间比率尚且不足 70%,而对于研发创新产品,该数值甚至不足 30%。过长的换产时间阻碍了生产的小批量化,急需对表贴设备的换产作业进行改善。以混频器为例,具体的换产作业改善如图所示。
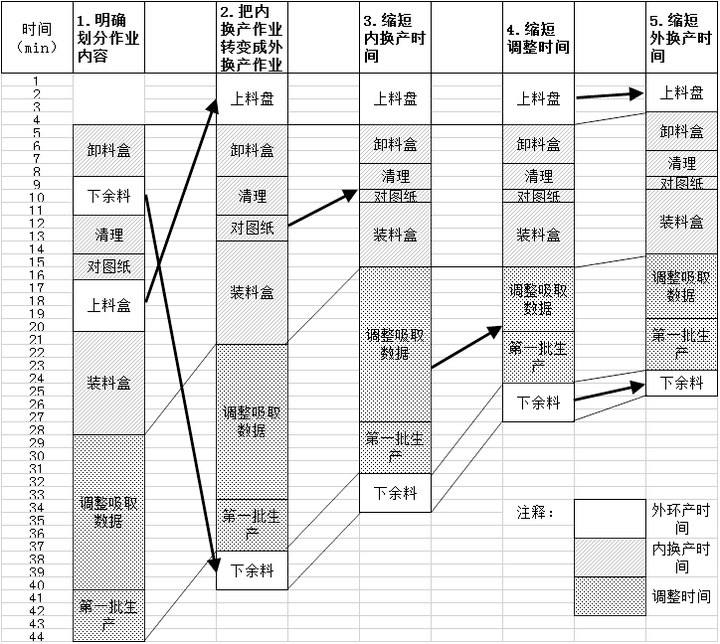
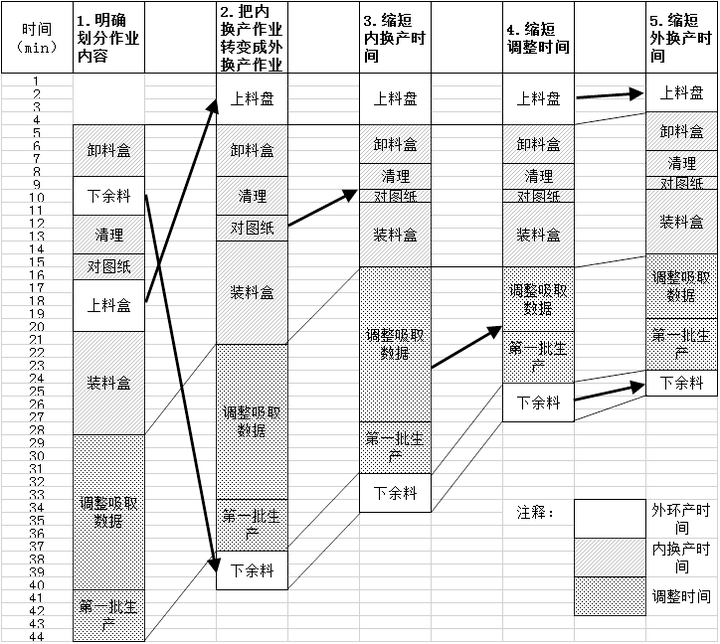
量产产品的换产时间从原有 40′30″ 减少至 20′,换产时间降低了 50%。对于创新产品换产时间的改善则通过建立研发创新产品的生产数据库,记录各产品核对图纸的关注点及生产程序,为相似创新产品的生产提供依据,创新产品换产时间由原有 3h 下降至 1h,换产时间降低了 66.7%。
三、计划排产改善——定定排产
板级线的目标是在保证量产半成品生产的同时尽可能多的生产研发创新产品。生产小批量化后,为实现生产的均衡化,对现有排产方式进行优化,引入定时不定量与定量不定时相结合的定定排产方式进行板级线排产。通过 pq 分析找到生产时间较长的品种并绘制帕累托图,并以此确定不同品种的每周生产计划。量产产品的生产时间超过了总时间的 80% 时,采用定时不定量的方式,即每天安排固定的时间生产这两种产品,生产数量由前一个周期内消耗的数量决定。研发创新产品项目,其每周需求量较小,换产时间较长,所以达到一定的最小表贴批量后才进行生产,尽量保证每个工作日完成尽可能多的研发创新产品的生产,其生产方式为定量不定时。利用定定排产方式对两台表贴机的周计划排产如图所示。
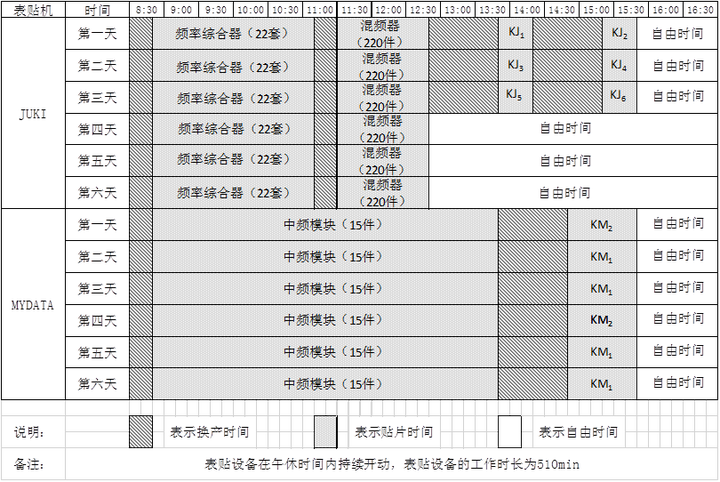
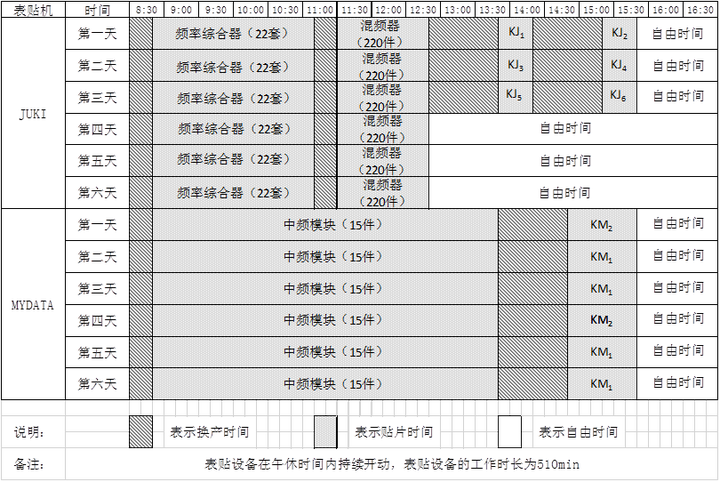
四、作业改善——基础 ie 动作研究
经过换产改善和排产优化,板级线中的表贴机能够及时地完成分配的任务量,并有充分的自由时间处理紧急插单情况,但表贴工序不仅仅包括表贴机的设备运转,还包括表贴工作的大量手工准备工作,通过秒表测时测定,员工作业中存在等待和动作浪费,因此对表贴工作进行作业改善。
表贴工作内容包括:扶正、方向检验、装盒、装料、换料、准备物料、刷焊膏及表贴等。改善前共有五人分工进行表贴工作,经过秒表测时,各作业人员的循环时间 ct 最短为 67 秒,最长为 309 秒,各作业人员的作业时长并不匹配,存在空手等待现象。另外,负责换料的员工 c 在一个循环内需要走动 9 米。改善前表贴机所用料盒摆放在工作台上,不便于装卸料盒。利用山积表将各员工的工作内容进行重新划分,将原有 b 员工的方向检验工作划分给 a 员工,装盒工作划分给 d 员工。将 b 员工节省出来做专职换产准备工作。通过增设一套料盒小车,将料盒按顺序摆放在料盒小车上,并放置在表贴机旁,减少装卸料盒的走动距离及操作时间。整合原有整理备料台与印刷台,减少了换料人员的走动距离至 4 米,降低了员工的疲劳程度。改善前后的表贴作业对比图如图所示。
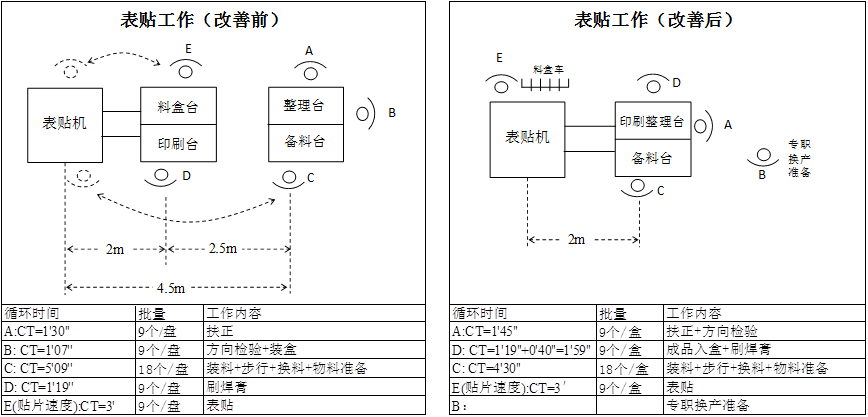
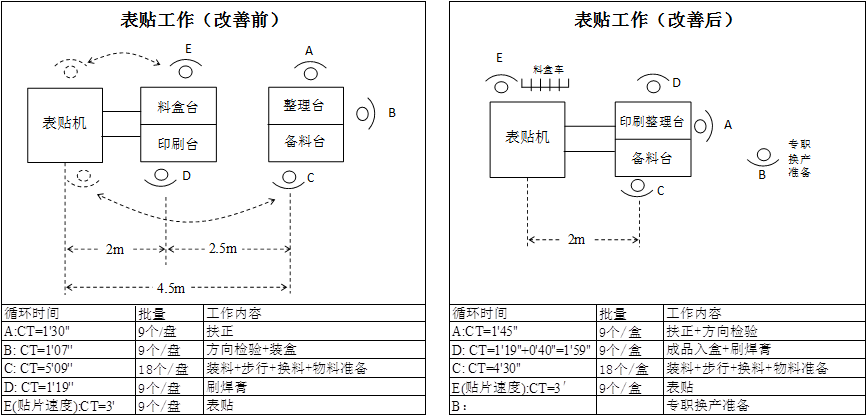
最终取得的改善收益如下——
「生产线整流化」
量产产品与创新产品在各工序的工作区分清晰,各产品的流动关系明确,生产现场的运行状态一目了然,降低了不同工序间信息的反馈难度,减少了产品停滞时间、在降低人数的情况下提高了产能,下图为改善后的物与信息流动图。
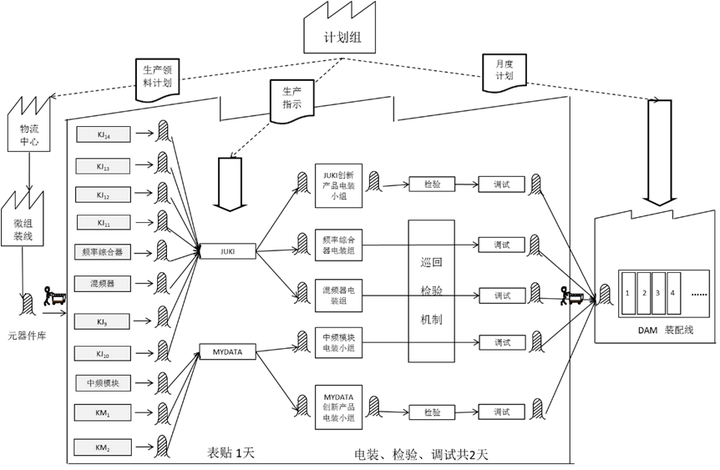
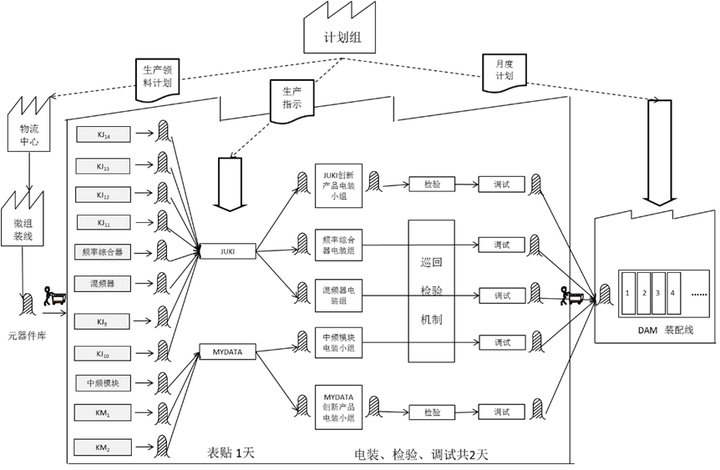
「电装效率提升」
对量产产品效率由原来的 300 秒/个提高到 280 秒/个。操作人员由现有 4 人减至 3 人,提升了电装效率的同时实现了少人化。
「表贴的换产时间降低」
量产产品的换产时间从原有 40′30″ 降低至 20′,减少 50%,创新产品换产时间从 3h 下降至 1h,降低 66.7%。
「板级线排产批量降低」
量产产品的表贴批量从两周需求量下降至每日需求量,排产批量降低 91.67%,减少了在制品库存和管理难度。按照定定排产的方式制定板级线的生产计划,保证每周生产任务完成的同时,留有一定的自由时间进行设备保全、员工培训或处理紧急插单情况,拖单比率降至 0。
「后补充机制的建立」
后补充机制的建立后,混频器的生产过程周期从原有的 17 天降低至 3 天,量产产品生产过程周期降低 82.4%。创新产品过程周期时间平均从 14 天降低至 7 天,降低 50%。
「操作人员数量减少」
对表贴工作进行时间测定,调整作业内容的分布,操作人员从 5 人减至 4 人,节省出的一人专职做换产工作。对电装工作进行测时及作业内容调整,提高作业效率的同时,操作人员由 4 人减至 3 人。
总结一下,对于多品种小批量产品而言,推行精益的过程要基于改善的理念,从生产方式出发,转变原有的计划式生产,建立后补充生产方式,实现后工序按需拉动式生产。通过将内换产作业转化为外换产作业,缩短调整时间,减少设备停止时间,进而实现缩短换产时间为实现小批量打下基础。通过量产产品定时不定量与创新产品定量不定时相结合的定定排产方式,最终实现生产的均衡化排产,解决了拖单和插单的问题。针对各工序作业进行相应的作业改善,进一步提高生产效率。
现如今,以精益为基础,数字化为导向的制造企业变革大幕已经徐徐拉开。在不断实现工业 4.0 的方向指引下,不断提升工厂的精益化水平,力争为客户提供高品质、低成本的产品。而对于工厂而言,无论产品批量和种类的数量如何变动,精益的初衷应是思考事物本身具有的样子,通过持续地对比现实与理想状态,采取根本性的改善措施以达到最终的目标。随着精益理念的不断发展,精益与管理越发交汇融合,精益的概念也逐渐演变为精益管理的思想,成为了一种人们社会工作的行为模式。通过一点一滴精益化的「行为方式」,我们开始影响大脑产生精益意识,最终实现人的精益化。而人作为企业的最核心资产,人的精益化才是企业持续改善和进步的最根本动力,才是能确保企业长盛久衰保持竞争力的根本。